Screw is a plasticized part of plastic processing machinery, and the quality of screw structure will have a key impact on plastic processing. The screw is a cylinder with a certain length of thread from the appearance, which seems simple and uncomplicated, but the change of plastic from the whole plasticizing process on the screw is quite complex. In the process of plastic transportation, there are pressure generation, energy transfer and conversion, and plastic state change. Therefore, the design of screw is particularly important. Through this introduction, I believe you will have a deep understanding of screw design.
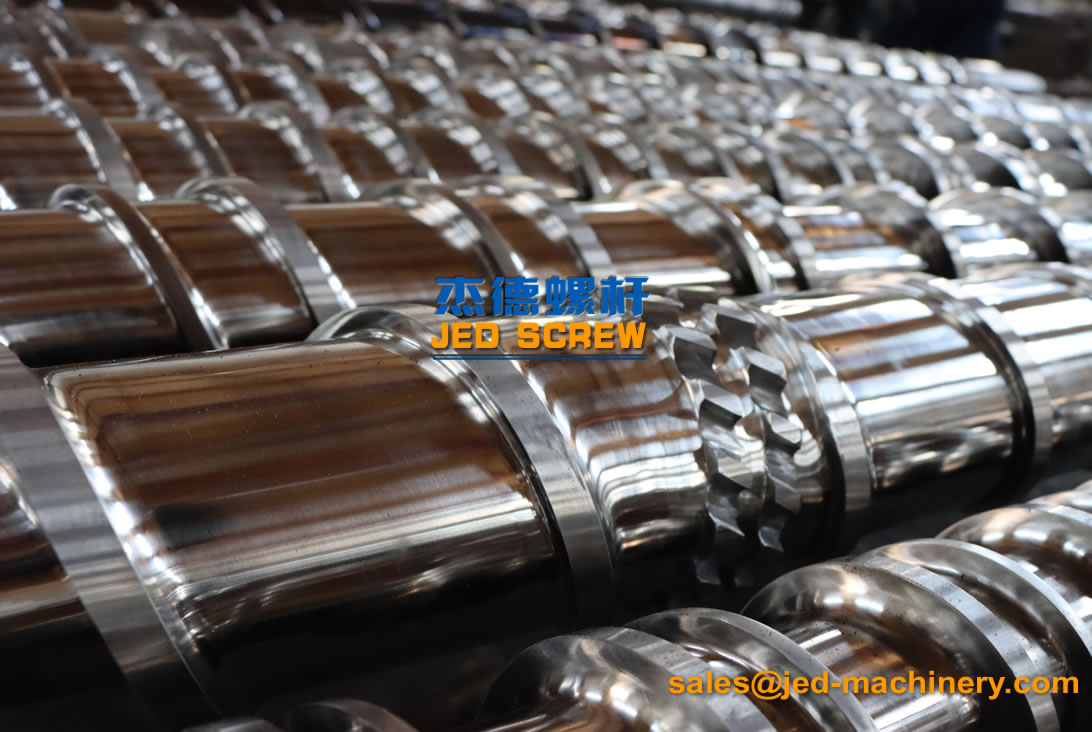
Basic parameters of screw
Screw design includes structural design and parameter design. First of all, we introduce the basic parameters of the screw, as shown below:
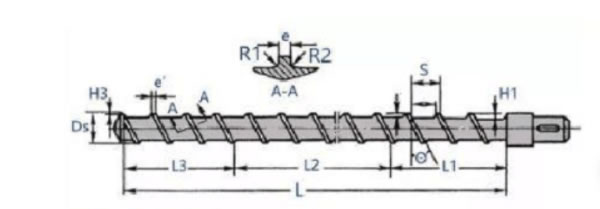
L: Total length of thread segment
L1: The feeding section
L2: compression segment
L3: Discharging section
H1: Depth of screw groove in feeding section
H3: depth of screw groove in discharging section
Ds: screw diameter
S: lead
e: width of screw edge
R1: arc radius of the propulsive surface
R2: back arc radius
Empirical values of common parameters:
Ds=S: screw diameter is equal to lead value
e=0.1*D: the width of the screw edge is equal to one tenth of the diameter of the screw
ε=0.93*H1/H3: compression ratio is the ratio of screw groove depth between feed section and discharge section multiplied by 0.93
R1 =( 1/2 – 2/3) * H3, and R2 is two or three times R1
Note: Usually R1 is a multiple of 0.5 and not less than 1
For example, given that the screw diameter is 45 mm, H1=6.0, H3=2.5, then we can calculate that the screw lead is 45 mm, the screw edge width is 4.5 mm, and the compression ratio is 2.23
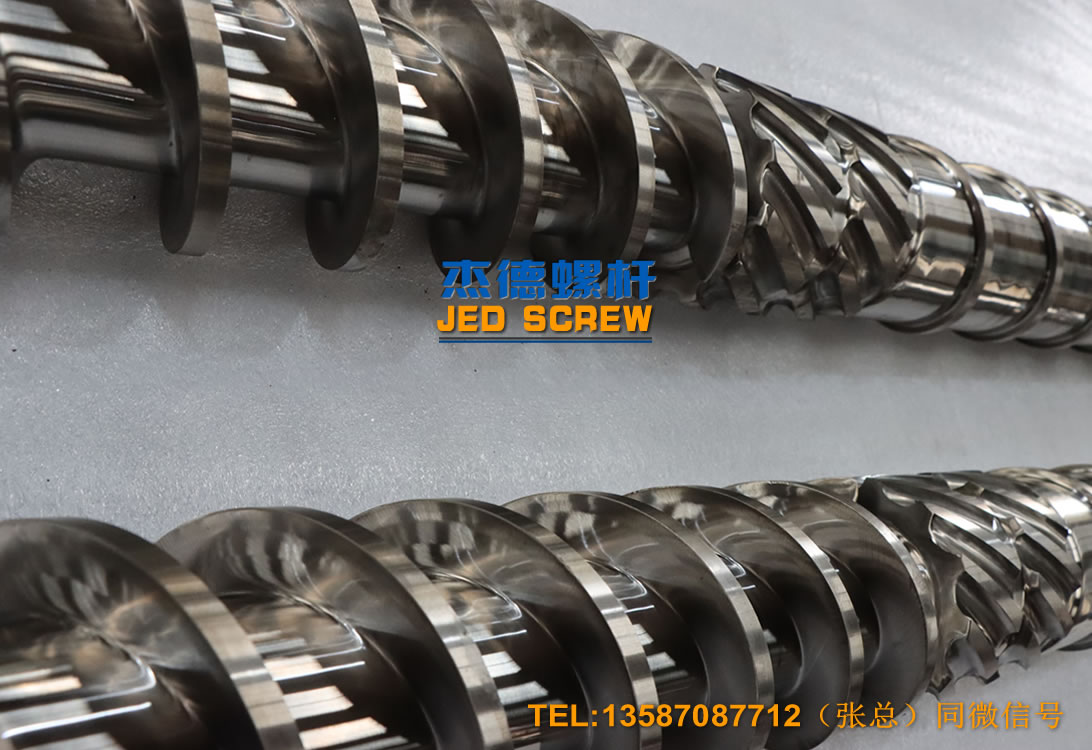
Screw three-section length distribution
The classic screw design is often referred to as the three-stage screw, which is the feeding section L1, the compression section (melting section) L2 and the discharge section (metering section)L3. So how are these three paragraphs divided? Since most of the plastics we usually use are amorphous plastics, the common screw three-section distribution parameters only need to remember the amorphous type:
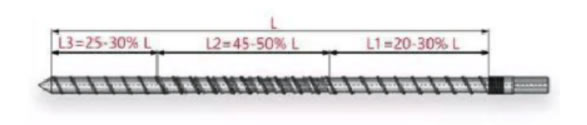
Simple memory, the compression section accounts for half of the total length of the thread section, the discharge section is slightly longer than the feed section.
Common plastic compression ratio experience value
PE: 3-4
PET: 3.5-3.7
HPVC (particle) : 2.5
HPVC(powder) : 3-4
PS: 2-2.5
PP: 3.7-4
PA66:3.7
ABS: 1.8
The length of three sections, screw lead, width of screw edge, depth of screw groove and compression ratio of feed section and discharge section are determined, and the conventional universal screw parameters are set. But the actual use of the screw and barrel should be considered, the gap between the screw and barrel is also an important parameter.
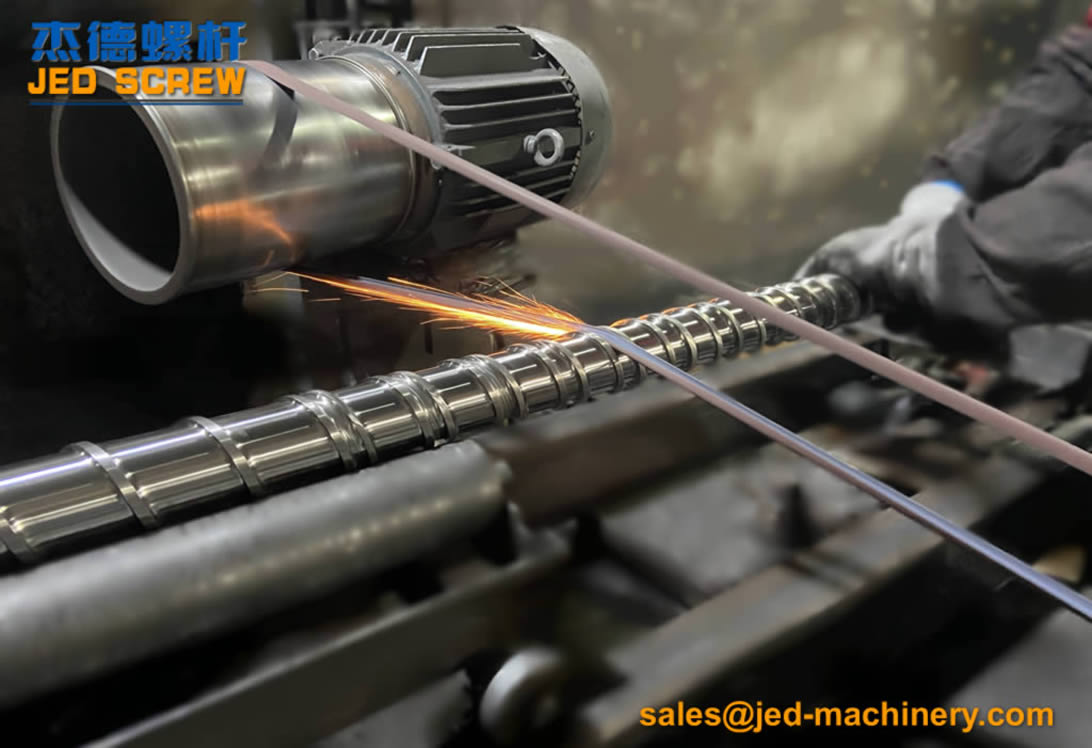
Factors considered for gap selection:
Ⅰ. Properties of materials to be processed (such as heat-sensitive and non-heat-sensitive materials)
Ⅱ. Nose resistance. The greater the resistance, the smaller the gap
Ⅲ. Material and heat treatment of screw barrel
Ⅳ. Machining conditions
Ⅴ, the diameter of the injection molding machine screw to select. Generally speaking, the larger the diameter of the screw, the larger the absolute value of δ should be selected; The smaller the screw diameter, the smaller the absolute value of δ should be selected. The selection of the gap δ between the screw and the barrel is a comprehensive problem, which must be considered comprehensively by combining various factors.
The gap between the screw and the barrel δ : the gap between the screw and the barrel is a very important structural parameter of the extruder, the gap size has a great impact on the amount of glue, because the leakage flow is proportional to the third square of the gap. Therefore, in order to ensure that the screw and barrel do not touch, the gap should be as small as possible. Usually the gap is 0.002D.
Select the diameter gap value of the existing extruder series, which can be selected according to the situation. δ= (0.003-0.005) *D takes the small value if the diameter is large, and the large value if the diameter is small.
Experience value of clearance (minimum clearance ~ maximum clearance) (mm)
Screw diameter 30: 0.10 ~0.25
Screw diameter 45: 0.15 ~0.30
Screw diameter 65: 0.20 ~0.40
Screw diameter 90: 0.30 ~0.50
Screw diameter 120: 0.35 ~0.55
Screw diameter 150: 0.40 ~0.60
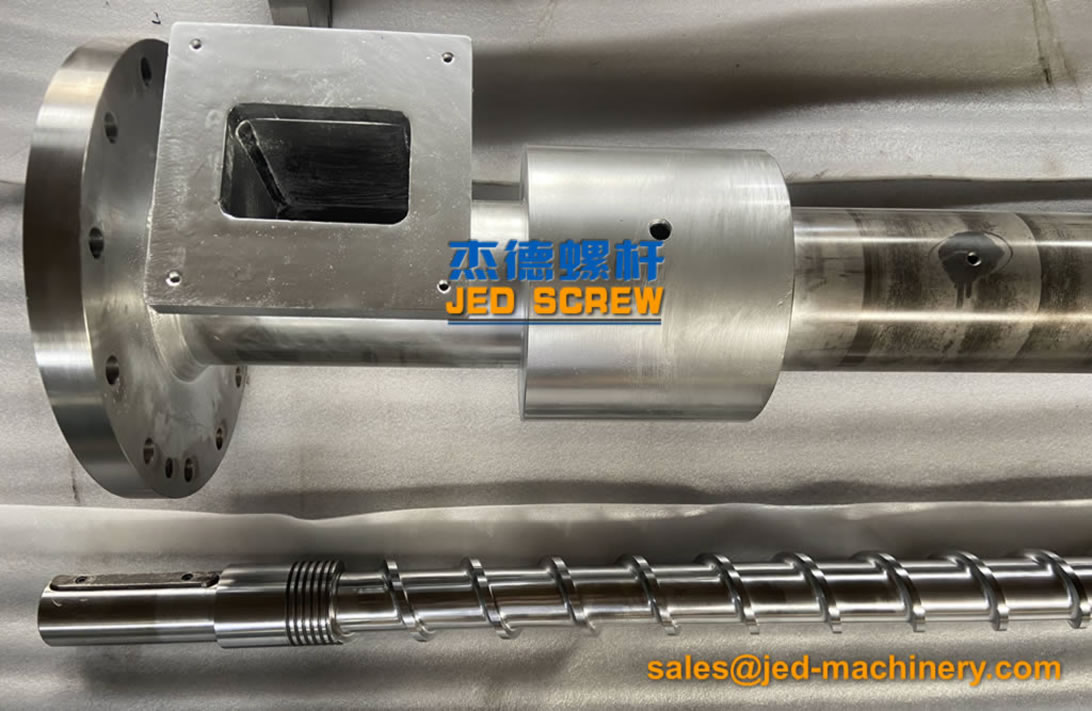
Separate BM screw with special screw design
In addition to the common three-stage classic screw design, in order to improve the mixing and plasticization effect in one step, there are a variety of common screw design with mixing structure. These mixing structures are mostly located in the head of the compression section and the metering section. Among them, the separated BM screw is one of the most common types.
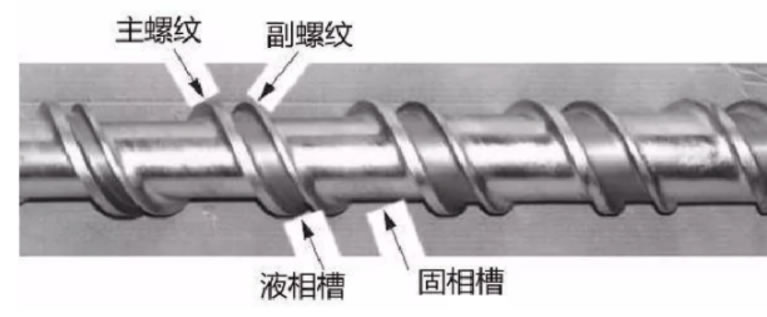
Separation screw (English name barrier screw or barrier flight screw) is a new type of screw developed on the basis of the common three-stage screw, and its basic mechanism is similar to the common three-stage screw. The difference is that the whole screw is composed of two sections of thread, which can be composed of front thread and rear thread with different leads, or main thread and secondary thread with the same lead. Because the molten film formed by solid phase melting crosses the gap into the liquid phase groove, the uncontained solid phase remains in the solid phase groove, forming solid-liquid separation, so the name of the separation screw.
Separate screw design parameter setting
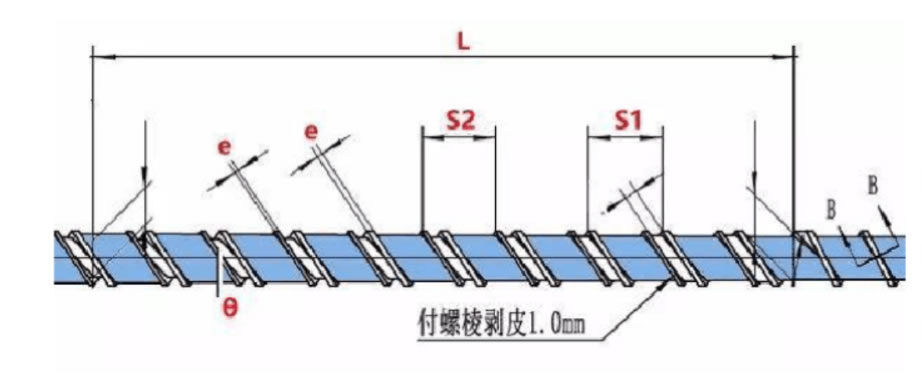
S1: lead of main thread
S2: secondary thread lead
e: width of screw edge
θ : thread rise Angle
The width of the main thread and the secondary thread of the common separation screw is the same, and the number of thread turns is different by one turn. Based on the same length of passage, the following equation is obtained:
ZS1+(2e+2K)/cosθ= (Z+1) S2
The formula for setting design parameters is derived as follows:
(S1-S2) Z = S2 – (2 e + 2 k)/cosθ
Where Z=L/S1
Note: K is the distance between the beginning of the secondary thread and the main thread, and Z is the number of turns of the main thread when the main thread and the secondary thread intersect, which is generally taken as an integer and then the value of L is derived.
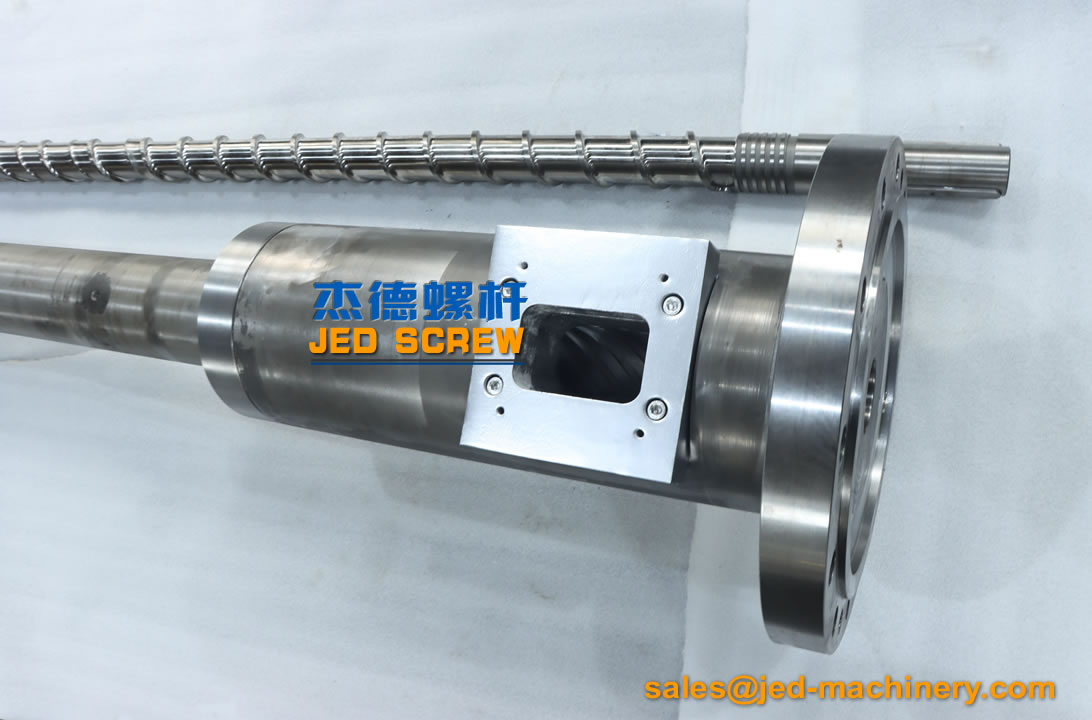
The separation screw has the following characteristics:
First, only the melted plastic can cross the gap into the liquid phase groove, and the small particles that have not been fully plasticized can also be fully plasticized under the action of high shear rate when passing through the gap. When the liquid phase is separated, the solid phase is directly in contact with the inner wall of the high temperature barrel to accelerate the melting of the solid phase.
Second,the length of the measuring section of the general screw is not equal to the theoretical length of the measuring section due to the different plastic, die pressure and operating conditions. On the separation screw, the liquid phase screw groove is all melt, so there is a stable measuring section length. In addition, the liquid phase screw groove and the solid phase screw groove are “sealed” by the screw edge, which reduces the reflux.
Three, in the separation type screw, the air between the solids and the water vapor adsorbed on the surface can be more convenient to escape from the hopper under pressure.
Four, there is no solid phase fracture problem, that is, there is no ordinary screw, because the broken solid phase fragments embedded in the gap between the screw and the barrel, and because of the irregular solid phase distribution around the screw caused by the screw radial pressure imbalance phenomenon.
The separation screw has a deep groove, so it has a small shear velocity gradient, and the melt is not easy to decomposition at high speed. This is also a reason why the separation screw can be opened to a higher speed and the quality can be guaranteed.
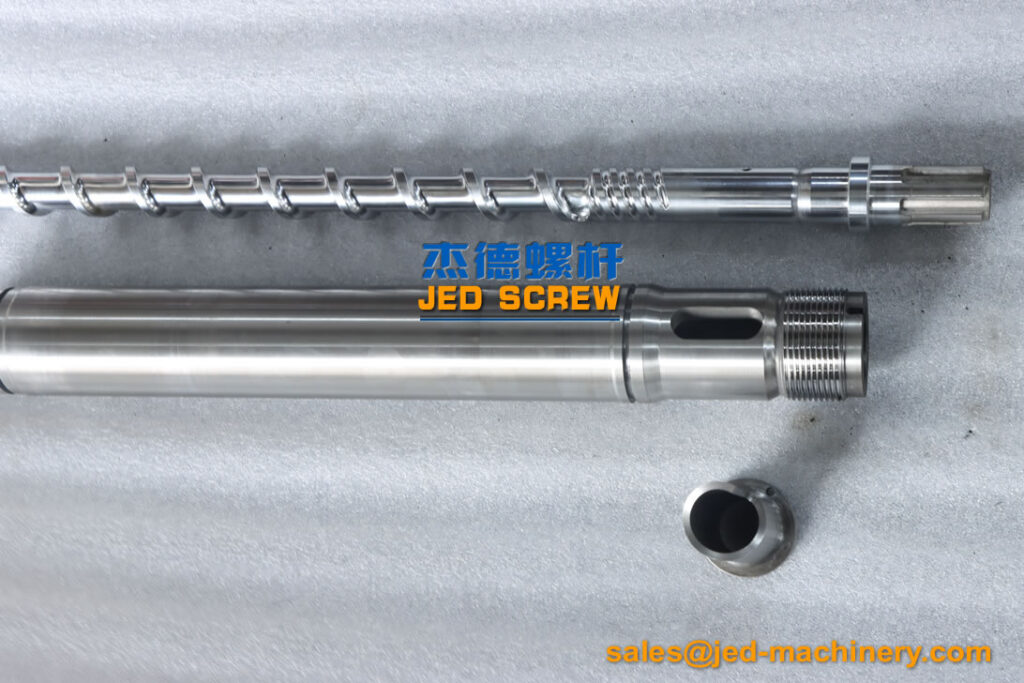
Zhoushan Jed Machinery Co., Ltd. is committed to the research and development, manufacturing, sales and after-sales service of injection molding machine and extruder precision screw barrel. According to the plasticizing characteristics of different raw materials, Jed company selects high-quality alloy steel, powder steel, powder stainless steel, with Jed processing technology, effectively ensure the product size accuracy and overall hardness, the majority of injection molding industry customers trust and recognition!
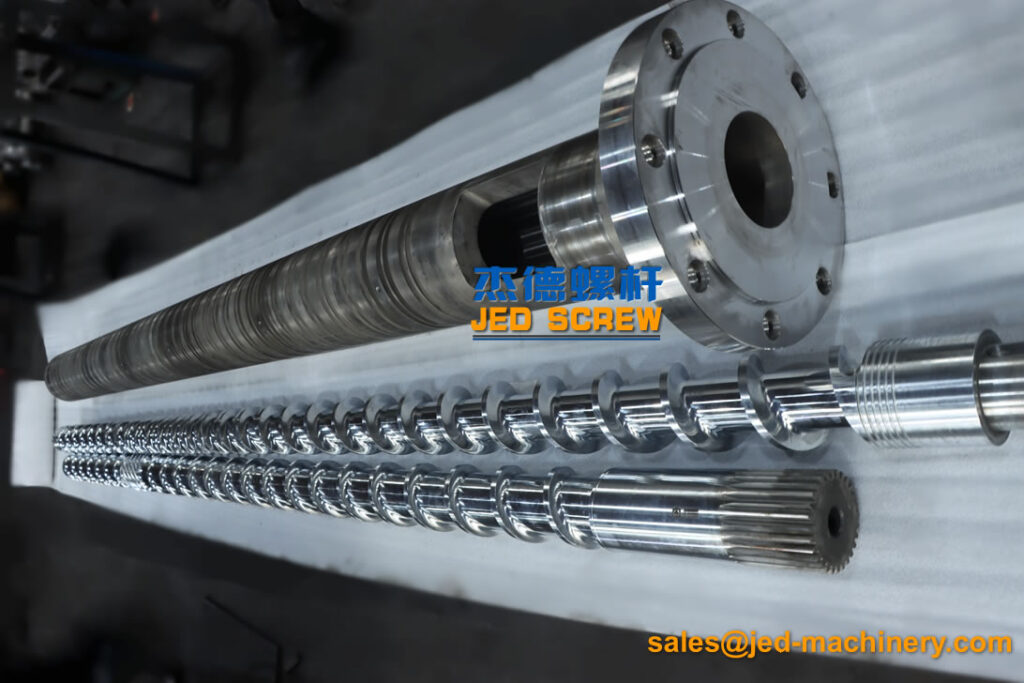
“Make plastic molding more stable and efficient” — is the mission and sense of honor of Jed people! Company address: No. 17, Zhenxing Zhong Road, Yancang Street, Dinghai District, Zhoushan City, contact number: +8613567672668 (WhatsAPP), wechat same number. Email:[email protected] .Welcome new and old customers to visit and guide!
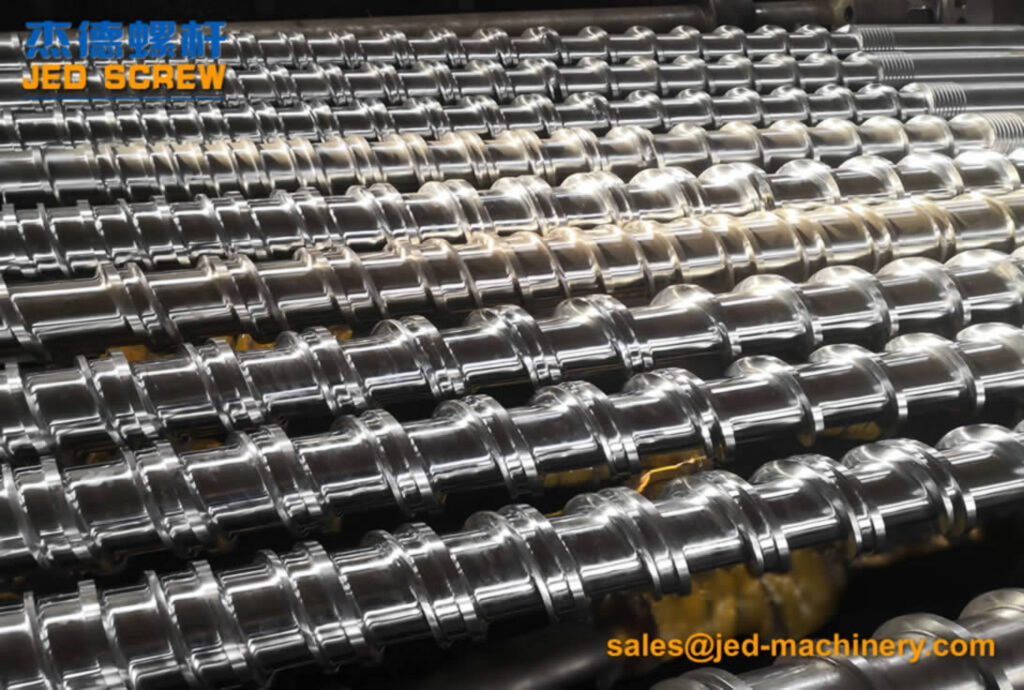
WhatsApp
Scan the QR Code to start a WhatsApp chat with us.