Product Introduction:
The traditional blow molding machine screw can be divided into three sections: feeding section, plasticizing section and separating section. The feeding section is also called the feeding section. That is, after the plastic is transported to the screw, with the rotation of the screw, this process is completed in the barrel, so the use of the barrel and the screw friction force to push the plastic in front of the compaction. The length of the feeding section is also related to the type of plastic, with different materials having different lengths. This is one of the functions of a blow molding machine screw. Plasticizing: The purpose of this step is to compress the plastic further, squish it hard, and then melt it into a liquid. From the feeding section to the plasticizing section, the plastic silently moves forward, passing through the screw groove, filter net, shunt plate and the head to block, forming high pressure. Slowly, gradually, being further compacted. At the same time, the raw material through the cylinder and screw rotation, mixing, shearing and other torture, so that the plastic gas fire three zhang, the temperature continues to rise, become liquid. But at this time, part of the body of the plastic is still solid, and the plastic slowly moves forward to the end of the screw. Due to the action of friction heat, the end of the screw is very high temperature. When the plastic reaches the end, it has become a viscous flow state. This is plasticizing. A more common name for a split segment is a homogenized segment. It is for plastics into the homogenization section, further plasticizing, constant pressure, quantitative, temperature and other ways to extrude from the screw. It is very important for the separation section in the production process, because the discharge speed of the whole melting section determines the production efficiency of the separation section. When the discharge speed of the melting section is slow, the separation section will give the rear leg, resulting in lower production speed. The problem is solved and the discharging speed of the screw is realized. In addition to the three sections, the expansion section is also added, which is installed between the plasticizing section and the separation section, so that the extrusion volume is larger and the production speed of the separation section is realized.
Our company is specialized in producing and manufacturing screw barrel for film blowing machine, which can be designed and customized according to customer needs and different plastic varieties. We have exquisite technology and rich experience, and adopt extremely hard wear-resistant materials, durable and plasticizing. High yield and energy saving. Sell well all over the world, efficient and timely after-sales service, let you feel at ease, rest assured, satisfactory!
Product Features:
1,it has the advantages of high wear resistance and corrosion resistance;
2, after special treatment, can effectively improve the wear resistance of the barrel screw, improve the service life;
3,cold and hot spraying hard metal process;
4,advanced nitriding technology;
5,bimetallic processing and manufacturing technology;
Scope of application:
Blowing low density polyethylene (LDPE), high density polyethylene (HDPE), linear low density polyethylene (LLDPE) and other composite films; Used for liquid, export, industrial products and other products packaging.
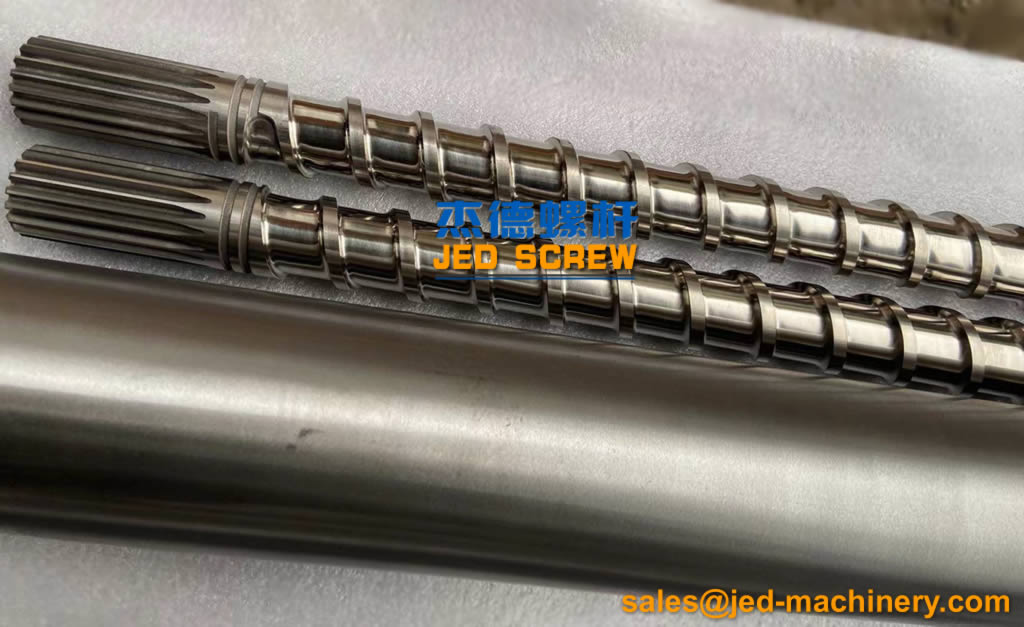
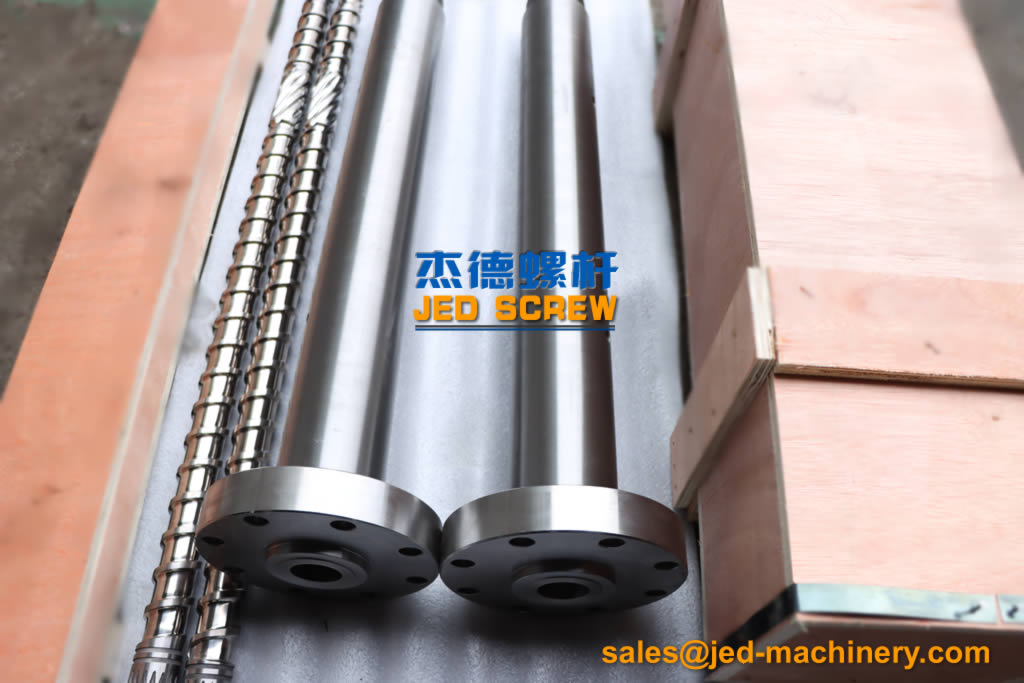
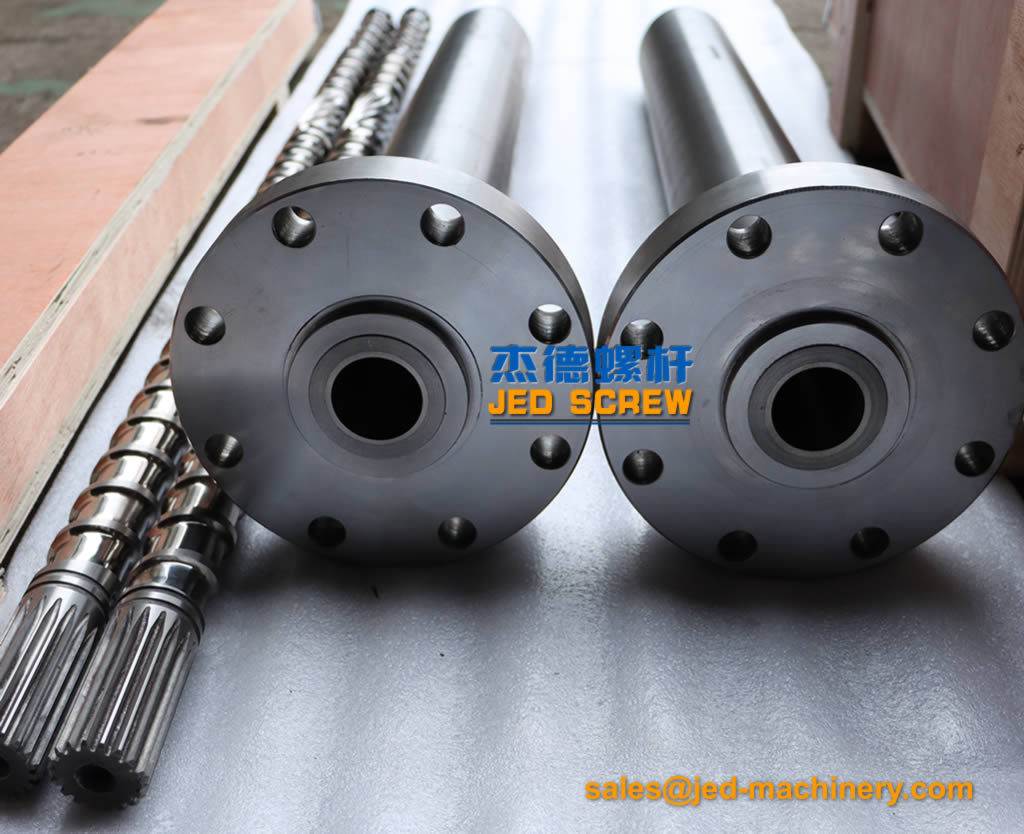
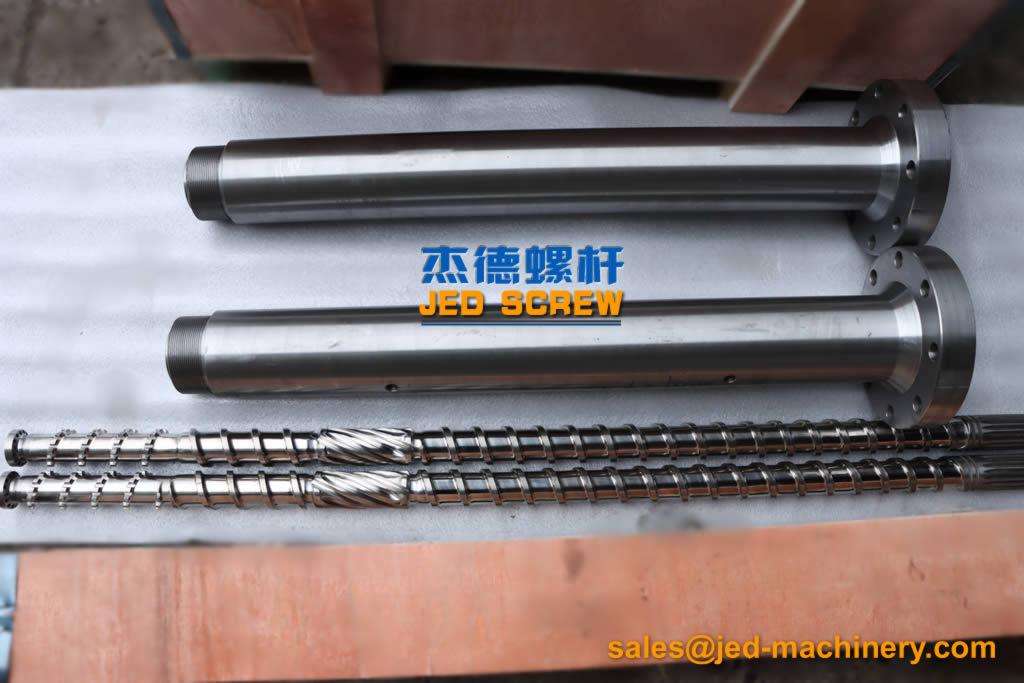
WhatsApp
Scan the QR Code to start a WhatsApp chat with us.