Product Introduction:
Spinning screw is an important part of melt spinning machine, which is used to transport, mix, melt into melt and quantitatively extrude solid polymer slices. Screw spinning, also known as “screw extrusion spinning”. The method of heating and melting the polymer into fiber by screw extruder. Polymer slices are added into the hopper of the screw extruder. Under the action of the screw extrusion, the polymer slices move forward, during which they are gradually heated and melted. Finally, after the spinning pump and spinneret assembly, the filaments are ejected from the spinneret hole, and then cured and wound. Direct spinning can also use screw as a melt conveyor. Such as for spinning polyester fiber, polyamide fiber, polypropylene fiber and so on.
Working principle:
Screw is usually divided into feed section, compression section and metering section. The length of each section is related to the nature of the material being processed. The polymer slice enters the screw groove from the barrel by its dead weight, and the screw turns in the sleeve driven by the motor to push the material forward in the screw groove. The material in the feed section is basically kept in a granular state. The initial part of this section needs to be cooled with water to prevent the material from melting prematurely and bonding, affecting the normal feeding. The latter part is the preheating area. The material absorbs the heat supplied by the external electric heater of the sleeve and begins to soften and partially melt. In the compression section, the screw groove gradually changes from deep to shallow, and the preheated material will melt and be compressed at the same time due to continuous heating, and the enfolded air will be discharged to the direction of the feed section. In the metering section, the compressed melt is further mixed and plasticized. After reaching a certain temperature, it is quantitatively transported to the box for spinning under a certain pressure. The viscosity and structure of the material in the screw extruder are complicated by the action of temperature and pressure, and chemical changes may occur in special cases.
Structural Features:
① Diameter D: it is directly related to the production capacity of the extruder. The diameter of the general spinning screw is 25 ~ 200 mm. If the diameter is too large, the heat transfer condition becomes worse.
② Length-diameter ratio L/D: is the ratio of the total length of the screw to the diameter, usually the series range of length-diameter ratio is 20~30. Working length L: refers to the sum of the length of feeding section, compression section and metering section. Large length-diameter ratio is conducive to the mixing and plasticizing of materials, the stability of flow and pressure, and the mixing and plasticizing of materials. However, too large length-diameter ratio will bring difficulties to the manufacturing and assembly, and also increase the bending deflection of the screw and make it easy to wear. The ratio of length to diameter of spinning screw for polyester and nylon is 24:1, and the ratio of length to diameter for spinning polypropylene can reach 27:1 or 30:1. The ratio of length to diameter of spinning screw should be 20-27 more, and the ratio of length to diameter of isotropic polypropylene should be increased to facilitate the mixing of color materials.
③ Compression ratio: refers to the volume ratio of each thread groove of the feed section and the metering section. Usually, according to the material characteristics (bulk density, compressibility), the compression ratio is 3 ~4. Usually, polyester takes 3.5~3.7, polyamide 6 takes 3.5, polyamide 66 takes 3.7, and polypropylene takes 3.7~4.
④ Pitch and thread section shape: the spinning screw adopts the equidistant screw which changes the groove depth. The groove depth varies within one pitch, called the mutant screw, suitable for processing of crystalline polymers with narrow melting temperature range and obvious viscosity changes, such as isotactic polypropylene, etc. Groove depth gradient called gradient screw, suitable for processing general polymer.
⑤ The clearance between screw and sleeve should be as small as possible. The clearance of small screw should be less than 0.002D and that of large screw should be less than 0.005D. The earliest melt spinning used a grate to melt polymer slices, which were then fused into a metering pump for spinning. Compared with molten grid, screw extruder has short melting time, large production capacity, suitable for spinning high viscosity melt polymer, melt quality is uniform and stable.
⑥ Type of screw: multi-head screw and variable pitch screw is mainly used for discharging, spinning screw mostly with single head screw of equal pitch, with short zone gradient screw is the most widely used. In order to improve the uniformity of the melt, a “torpedo head” or a mixing head can be installed on the head of the screw to increase the mixing effect. In addition, there are additional mixing elements of the pin screw, change the screw groove structure of the separation type screw, shear barrier section of the barrier type screw, vacuum exhaust screw, etc. The combined screw has separate secondary thread and barrier head or pin, which can greatly improve the efficiency of the screw.
Product Advantages:
The spinning screw specially designed and manufactured by our company is made of chrome-molybdenum alloy heat-resistant stainless steel, which is treated by ion nitride and polished. It has sufficient strength and stiffness, good wear resistance and thermal conductivity, corrosion resistance and small thermal deformation.
“Made for you” is the company adhere to the unchanged characteristics, to meet customer requirements, provide technical design, site mapping, renovation and other services, in the first time for customers to create more, greater economic and social benefits. We continue to absorb advanced production technology, scientific management system and timely market information, and strive to make their products and the development of the world machinery synchronization. To help you succeed is our most solemn commitment! For your service, we are not afraid of difficulties! Good project, we do everything! [Jed Machinery] and you hand in hand to create a better market tomorrow!
Scope of application:
Melt spinning of PET, PA6, PA66, PP slices; Chemical fiber extruder and non-woven fabric extruder; Wet spinning machine, melt spinning machine, dry spinning machine; Viscose fiber, acrylic fiber, Vinylon and other spinning; Spinning equipment for polyester, polyamide and polypropylene; Filament production of acrylic and Vinylon;
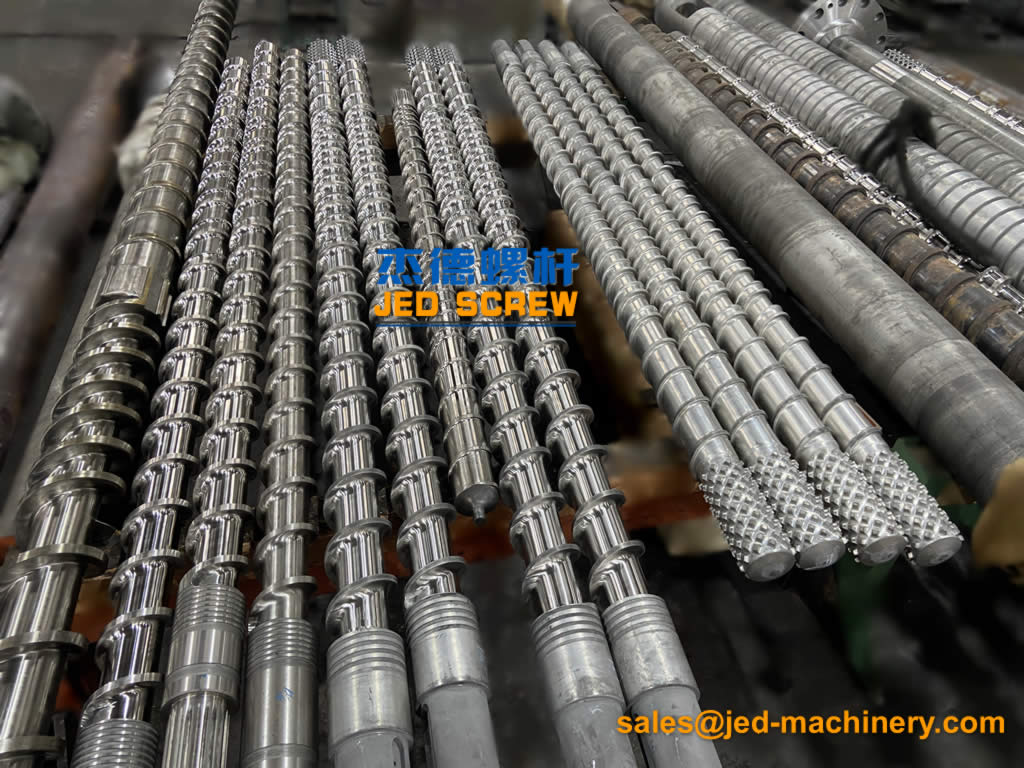
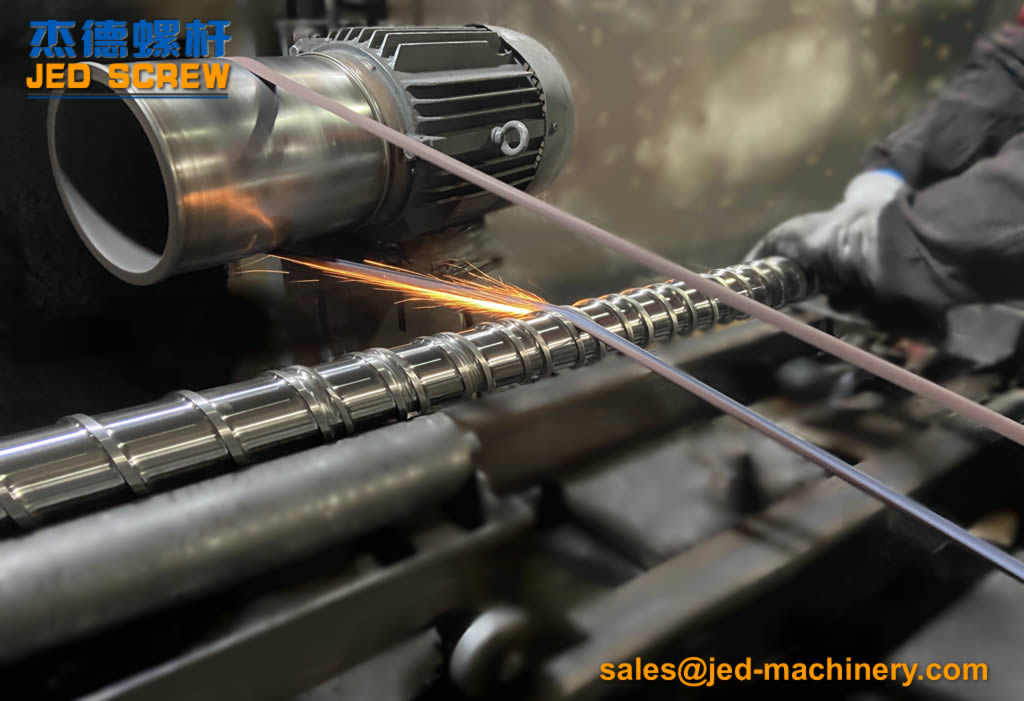
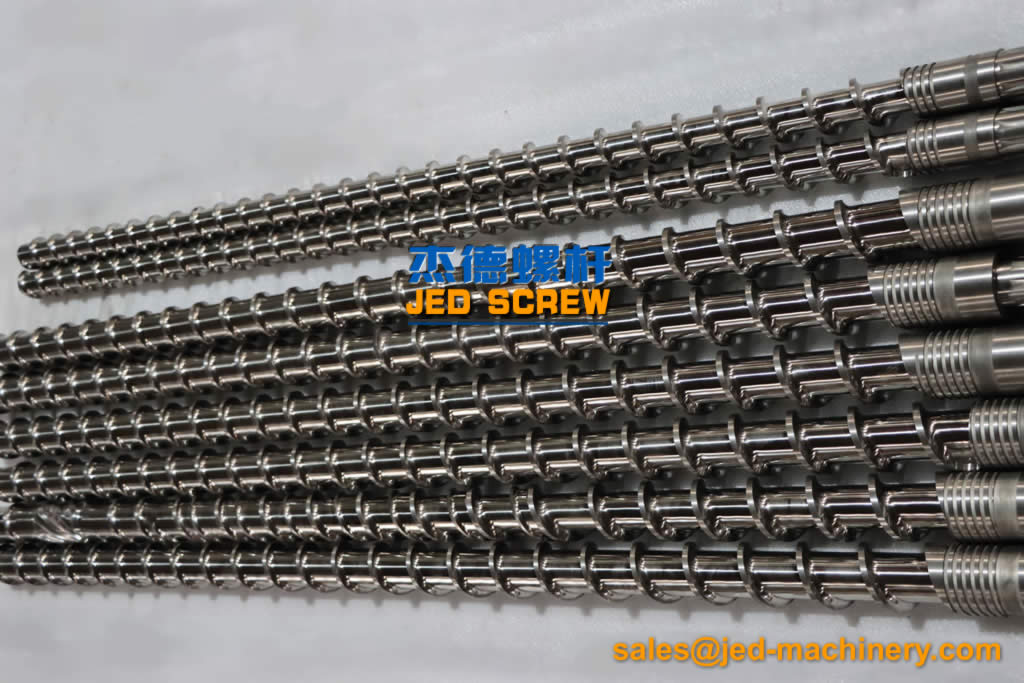
WhatsApp
Scan the QR Code to start a WhatsApp chat with us.