Product Introduction:
The field of plastic power cables is developing towards the direction of high voltage, ultra-high voltage, large length and large capacity, in-depth research on insulation thinning, and strengthening the development of heat-resistant, age-resistant, oil-resistant, chemical-resistant, fire-resistant, halogen-free, low-smoke, flame-retardant and non-toxic cables.
Extrusion machine consists of extrusion system, transmission system, heating and cooling system. The extrusion system includes screw, barrel, hopper and die, etc. The screw is the main part of the extruder and is made of high strength and corrosion resistant alloy steel. The barrel is a metal cylinder made of heat-resistant, high-strength, wear-resistant and corrosion-resistant alloy steel or composite steel pipe. Its length is 1530 times its diameter to allow the plastic to be fully heated and plasticized. The casing is equipped with resistance wire or induction heating pipe, temperature measuring element and cooling pipe. The plastic extrusion process is carried out by a single screw extruder in a continuous extrusion mode. Check material → heating screw → material preheating → add hopper → from preheating section to plasticizing section → homogenizing section, after barrel heating, shearing, friction → plastic constant temperature, constant pressure, quantitative push to the machine head → mold core, mold sleeve molding. The aspect ratio is the ratio of the length of the screw to the diameter of the screw. The large aspect ratio makes the plastic mix fully, the plasticization is good, the extrusion pressure is large, and the screw rotation and extrusion volume can be improved. The screw is cooled by central water. In order to eliminate the excess heat generated by shear friction of screw rotation, avoid excessive temperature to make plastic decomposition, scorching and shaping difficult. At the same time, it can improve the conveying rate of materials, stabilize the amount of glue, and improve the quality. The barrel is divided into water – cooled and air – cooled. Small and medium-sized extruders generally use air cooling; Large use water cooling or a combination of the two.
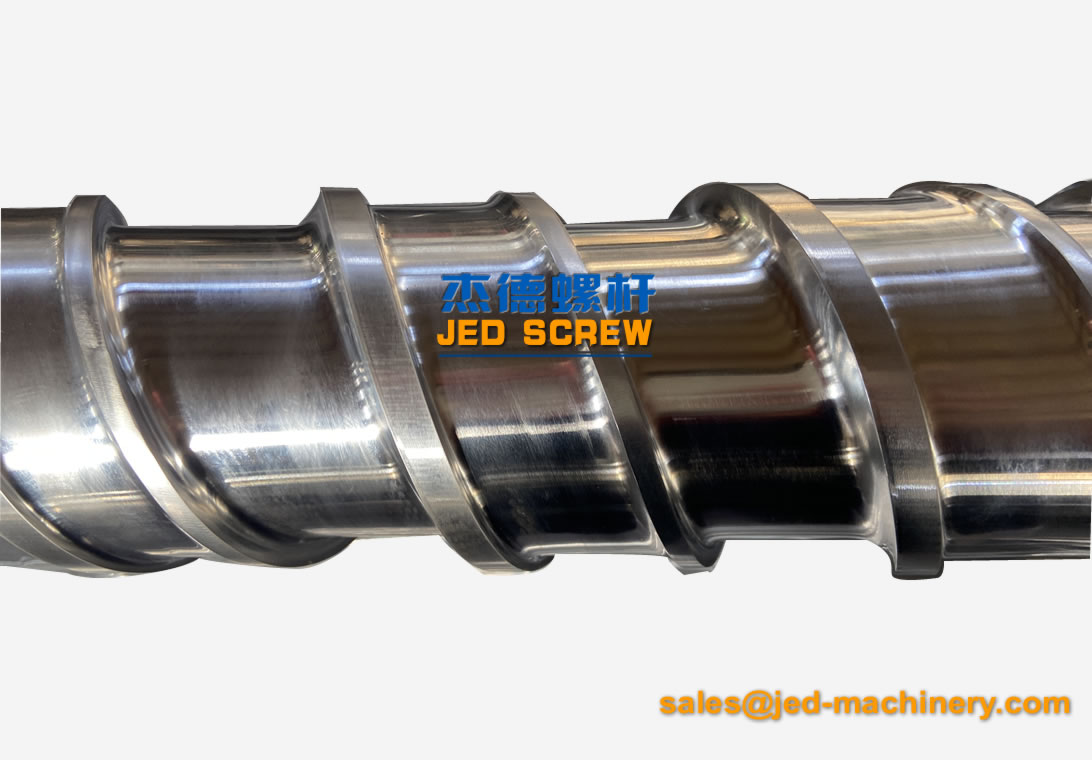
Screw selection:
The screw is the core of the extruder, with gradual deformation (isometric depth and isometric depth) and isometric mutant type, the former often extruded PVC (75~180℃), the latter often extruded low density PE(120~150℃).
Screw is divided into three sections, feeding section of plastic compaction and transportation; The compression section further compacts the plastic, makes it heated and plasticized, and all becomes viscous flow state; The homogenization section further plasticize and homogenize the viscous fluid transportation, and extruder from the machine head at constant pressure, quantity and temperature. The segments are of different lengths.
Small screw for small plastic machine, screw diameter of 45mm and below, using equal distance and depth of full thread screw, extrusion speed;
The diameter of medium screw is 60~120mm. Full thread screw with gradual thread depth, equal pitch, from shallow to deep, large amount of glue, fast extrusion speed, good plasticization.
Large screw diameter 150mm and above, used for the production of large section cable. Φ150 extruder and Φ200 extruder adopt large screw with equal distance and different depth; The large screw of Φ250 extruder is divided into three sections, namely equal depth and unequal distance, equal depth and unequal distance, the compression ratio is 2 ~ 3, and the aspect ratio is about 15:1.
Separation screw is in the screw melting section of the screw edge in the addition of an auxiliary screw edge, artificially divided into melt tank and solid tank, to avoid the plastic and melt mixed together, can make the internal pressure increase, small reflux, large amount of glue, strong adaptability, has been widely used.
Main parameters of screw
The main parameters of the screw are the diameter of the screw, the ratio of length to diameter, the ratio of compression, the pitch, the width of the screw groove, the depth of the screw groove, the screw Angle, the gap between the screw and the barrel, etc.
1,The diameter of the screw is the outer diameter of the thread. The extrusion volume of the extruder is approximately proportional to the square of the screw diameter, which has a great influence. Therefore, the screw diameter is often used as the extruder specification.
2,Screw aspect ratio is the ratio of the length of the working part of the screw to the diameter of the screw. Processing PVC using aspect ratio 20; Polyolefin is 25.
3,The compression ratio is the ratio of the volume of the first screw groove in the feeding section to the volume of the last screw groove in the homogenization section. Increasing the compression ratio is to make the plastic fully plasticized and compacted. Using ordinary screw, low density PE, soft PVC compression ratio of 2~3; Hard PVC compression ratio of 2.5 ~ 4.5; High density PE and polypropylene compression ratio of 3 ~ 5. Using separation screw extrusion soft PVC and polyolefin compression ratio of 1.9 ~ 2.0, the current common use is equal distance unequal depth screw.
4,The spiral Angle is the Angle between the thread and the screw cross section. The spiral Angle is too large, the feeding path is short, the plasticizing time is short; If it is too small, the thread is dense and the extrusion amount is small. For the feeding section, the screw Angle of 30 degrees is suitable for powder, 15 degrees is suitable for square granule, and 17 degrees is suitable for spherical and columnar granule.
5,The gap between the screw and the barrel is half of the difference between the inner diameter of the barrel and the outer diameter of the screw (the distance between the outer surface of the screw and the inner surface of the barrel). If the clearance is too large, the reflow plastic will overheat and decompose. The general clearance is 0.1 ~ 0.6mm;
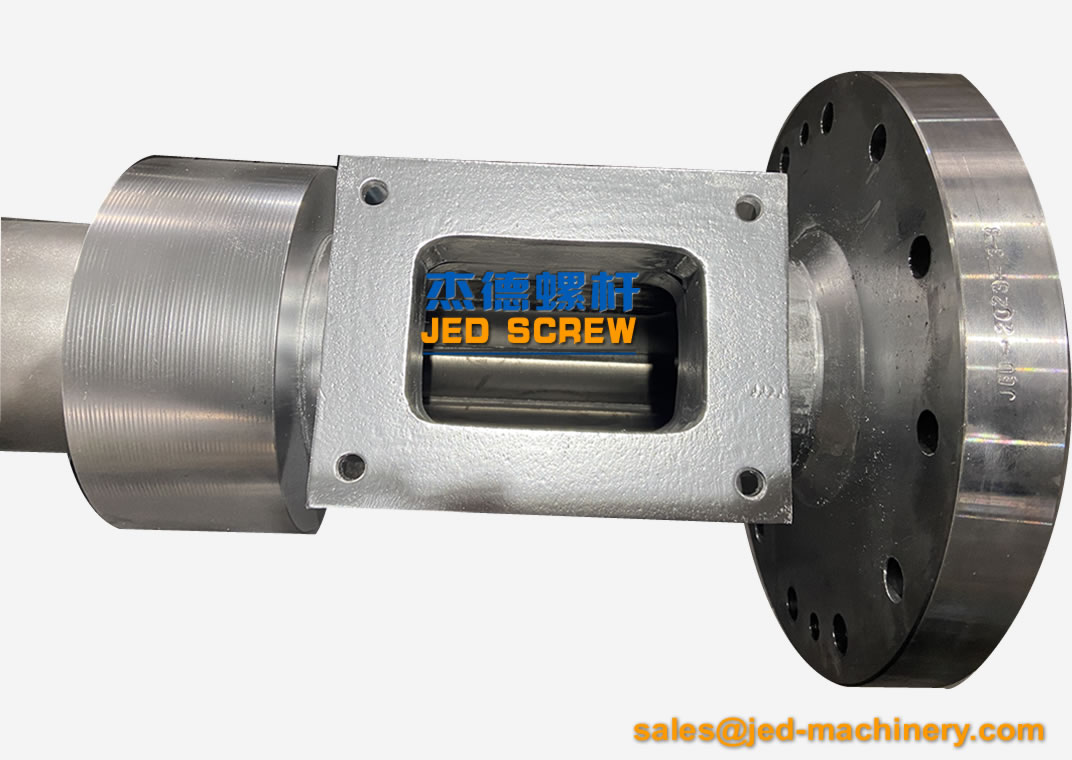
Section and description of screw
1) Feeding section (also known as preheating section), this section of the screw surface smooth, deep thread. Function: preheating and heating, compaction and transportation of plastics. The length of the feeding section is related to the type of plastic, and the extruded crystalline polymer is longer. Hard amorphous polymer followed by; Soft non-crystalline polymers are shorter.
2) Plasticizing section (also known as compression section) has shallower threads than feeding section. Function: further compaction and plasticization of plastic, discharge of air in plastic. The thread is gradually shallow, the filter screen, porous filter plate and the machine head produce resistance, and the plastic produces high pressure to be compacted; The outer heating of the barrel and the screw make the plastic stir, mix and shear in the barrel and melt into viscous flow state; PVC plasticizing section length (up to the full length of the screw), PE accounts for about 45-50% of the full length of the screw.
3) The homogenization section (also known as melting section) makes the plasticization of viscofluid plastics more uniform. Driven by screw stirring, it is extrudated from the machine head at constant pressure, quantity and temperature. This section accounts for about 20 ~ 25% of the total length of the screw.
Extrusion quantity and quality
Extrusion volume is an important characteristic parameter of extruder. The main factors affecting the extrusion volume are as follows:
① The greater the extrusion pressure, the smaller the extrusion volume;
② The shallower the groove, the more stable the extrusion volume; When the screw groove is deep, the extrusion pressure changes slightly, and the extrusion volume will fluctuate greatly;
③ The wider the groove, the greater the extrusion volume;
④ The thread is too shallow, the extrusion is small; If it is too deep, the extrusion volume will be unstable and the uniformity of plasticization will be affected.
⑤ Under the requirements of ensuring the extrusion volume, the screw speed should be improved, the depth of the screw groove should be increased to ensure the plasticization quality;
⑥ The gap between the screw and the barrel should be appropriate. If it is too large, the plastic is easy to produce reflux and leakage, the extrusion pressure fluctuation, affecting the extrusion amount, resulting in the plastic overheating scorching and molding difficulties.
Speed of screw
The speed of plastic extrusion needs to increase the screw speed, when increasing the extrusion speed:
1) The heating temperature must be increased to control the pressure of the machine head.
2) Extrusion speed is related to extrusion thickness, temperature and material.
3) The traction speed requires the traction speed to be uniform and stable, and the traction speed is unstable in coordination with the screw speed, which is easy to produce bamboo joints; Traction speed is too slow, easy to pile glue or produce empty tube phenomenon traction speed is too fast, easy to pull thin thickness or break.
Cooling of the screw
With the increase of screw speed, the plastic shear and friction in the barrel intensify and generate heat, easy to decompose and scorch. The screw should be cooled to avoid plastic decomposition and “skid” in the barrel; The cooling of the feeding section is conducive to the return of gas to the hopper and discharge; The homogenization section cooling, a layer of low temperature plastic will cover the bottom of the thread groove, objectively make the homogenization section of the groove shallow; The cooling medium can be water or air, depending on the length of the cooling pipe inserted into the screw to meet the cooling demand. Precautions for using cooling water:
1) The screw cooling water flow should not be too large and too cold, feel the water warm by hand;
2) The use of screw cooling water should pay close attention to the change of outer diameter, so as to control the cooling water;
3) Shutdown should stop water to prevent equipment accidents;
4) The cooling water of the screw should be handed over.
5) The cooling of the fuselage is mainly air cooling, especially the cooling of the homogenization section;
6) The cooling PVC of the product is cooled with cold water; Polyethylene, polypropylene with a step-by-step cooling method: the first section of 75 ~ 85℃, after the gradual cooling of each section, until room temperature. The smaller the temperature difference between sections, the better.
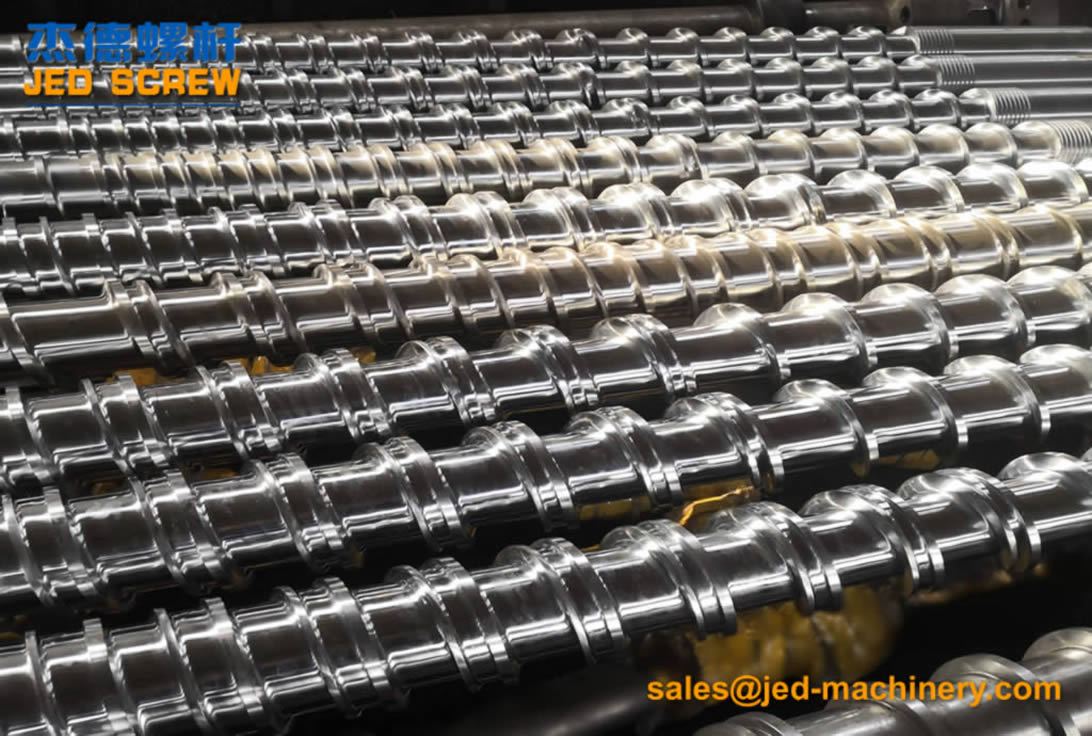
Screw maintenance
(1) Screw idling is not allowed;
(2) When cleaning the screw, the screw should be smooth, so as not to hurt;
(3) It is strictly prohibited to fall into the barrel, so as not to damage the screw;
(4) If the heating temperature does not reach the process temperature, it is strictly forbidden to start the screw;
(5) Shutdown should stop water, the temperature drops too low should stop cooling;
(6) Screw removal should be carried out in order: clean the plastic in the barrel → remove the machine head → push the screw out from the upper bearing at the place of adjusting the top rod and strictly prohibit hitting the root of the screw → take out the screw slowly. After taking out about 1/3 of the larger screw, it should be placed on the screw carriage in time → take out the screw completely to prevent falling on the ground;
(7) The order of installation is opposite. When the screw contacts the thrust bearing, the bearing and the screw should be matched well, and then the screw can be jacked into the thrust bearing, and then the machine head is installed, and the machine head is evenly and reliably pressed on the filter plate.
Scope of Application
Plastic power cable, plastic communication cable, plastic wire and cable extruder for electrical equipment; Extruder of PVC and polyolefin for insulating materials; Extrusion of power cables, cross-linked cables (including silane cross-linked cables and irradiation cables), overhead insulated cables, etc.
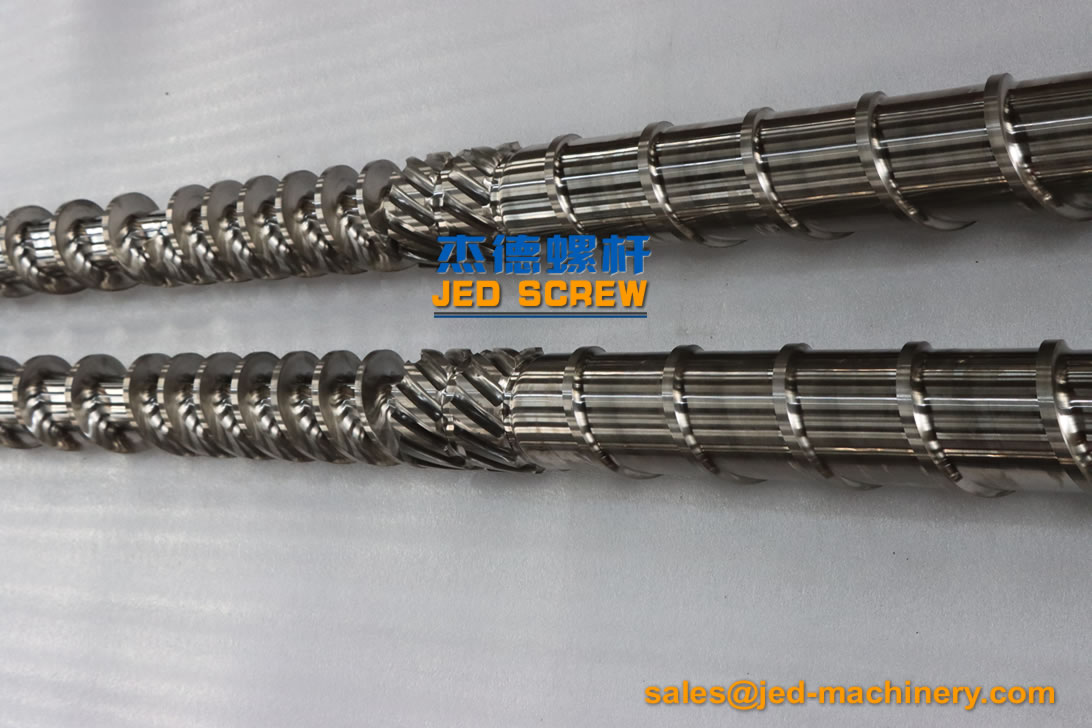
WhatsApp
Scan the QR Code to start a WhatsApp chat with us.