This paper is a hodgepodge of extruder and screw knowledge, from the extruder parameters, screw function, screw elements, extrusion process temperature, extruder screw speed and so on.
One, Extruder nameplate
It is important to know the extruder code and specification parameters, for example: SHJM-Z40×25×800 extruder, what does it mean?
Screw diameter 40mm, aspect ratio 25, traction roller length 800mm twin screw mixed plastic extrusion and plastic improvement film machine.
Brand meaning
1, “SH” is the category code, refers to the twin screw mixed type (also written: SHSJ, SJ refers to plastic extruder);
2. “J” is the group code, referring to extruder;
3, “M” refers to the variety code, refers to blow molding film machine;
4. “Z” refers to the auxiliary code, refers to the main unit, and “F” refers to the auxiliary unit;
5, “40×25×800” refers to the specification parameters, refers to the screw diameter of 40mm, length-to-diameter ratio of 25:1, traction roller length of 800mm;
6, the last digit is the manufacturer identification number, generally does not appear, is omitted.
Two, Extruder parameters
There are many parameters characterizing the performance of extruder and screw, the most common indicators are as follows:
1, “D” is the diameter of the screw, which is an important parameter to measure the output of the extruder;
2, “L/D”, refers to the screw length and screw diameter ratio, directly affect the degree of plasticization, is a sign of use, general plastic modification processing, with about 30-60, commonly used 35:1, 40:1 or 44:1;
3, “H”, screw groove depth, refers to the size of its material space;
4, “E” screw edge thickness, the size of the craft body now shear;
5, “6” screw and barrel clearance, extruder quality of an important parameter, generally in 0.3-2mm, over 5mm extruder is a warning line;
6, “N” host speed, refers to its highest value, refers to a processing adjustment range, greatly affects the output and the division of medium, high and low speed;
7, “P”, motor power and heating power.
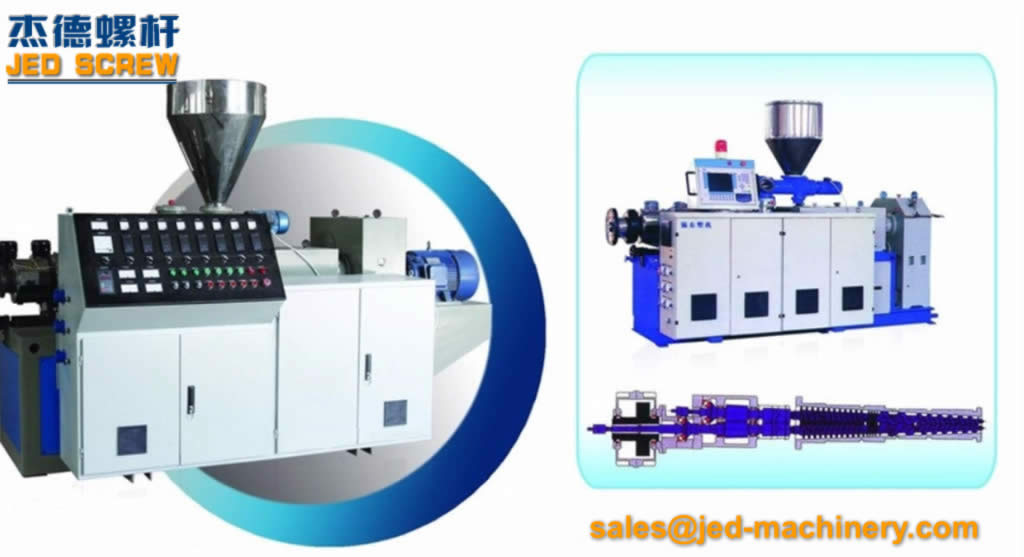
Three, Screw section and function
Screw is generally divided into: conveying section, melting section, mixing section, exhaust section, homogenization section of 5 sections, the specific functions are as follows:
1. Conveying section: conveying materials to prevent overflow;
2. Melting section: this section through heat transfer and friction shear, so that the material fully melting and homogenization;
3. Mixing section: the material component size is further refined and uniform, forming an ideal structure, with distribution and dispersion mixing function;
4. Exhaust section: discharge water vapor, low molecular weight substances and other impurities;
5. Homogenization (metering) section: conveying and pressurizing, establish a certain pressure, so that the material at the die mouth has a certain density, while further mixing, finally achieve the purpose of smooth extrusion granulation;
The difference between distributed and dispersed mixtures
Distribution mixing, so that the melt segmentation and reorganization, so that the spatial distribution of each component uniform, mainly through separation, tensile, distortion, fluid activity reorientation and other stress displacement flow.
By dispersing and mixing, the components can be broken into particles or the size of the two incompatible components can reach the required range, mainly by shear pressure and elongation stress.
Four, Threaded elements
In order to realize the function of each section of screw, need to use different thread elements, functional combination, commonly used thread elements for 2 categories.
Conveying element, threaded: method of representation, such as “56/56” conveying block, the previous “56” guide is 56 MM, the latter “56” refers to the length of 56 MM.
Generally, with the increase of the lead of the screw block, the amount of screw extrusion increases, the material residence time decreases, and the mixing effect decreases. Often said that the big lead, refers to the pitch of 1.5D~2D thread block, small lead, refers to the pitch of about 0.4D thread block, between the two for the middle lead thread element.
Rules of its use
1, large lead thread, mainly to transport, conducive to improve output, such as heat sensitive polymer, shorten material residence time, reduce degradation can be used.
Can also be used in the exhaust of the machine, the selection (also choose shallow groove) large lead thread elements, increase the surface area, conducive to exhaust, volatilization, etc.
2, medium lead thread, mainly mixed, with different working segments gradually reduced combination, used for conveying and pressurizing.
3, small lead thread, for the general combination is gradually reduced, used for conveying section and uniform metering section, to pressurize, improve melting, and improve the mixing degree and extrusion stability.
Mixing elements, including two categories: “K” series and “M” series (teeth)
“K” series: representation, such as K45/5/56 “, belongs to the shear block, with “K” refers to the flake shear block, “45” refers to the Angle formed by the pieces, “5” refers to the total of 5 pieces, “56” refers to the length of 56 MM, the width of the screw edge is 56/5 =11.2 MM).
Key points of thread element parameters
1, Direction: there are forward and reverse directions. In the opposite direction, the conveying of materials has an obstacle effect, play a role in prolonging the time, improving the filling and increasing the pressure, greatly improving the mixing effect.
2, Angle: generally 30°, 45 °, 60 °, 90 °, its role and effect:
Ⅰ. In the forward direction, increasing the staggered Angle will reduce the conveying capacity, prolong the residence time, improve the mixing effect, but the more prone to leakage flow.
Ⅱ. In reverse, increasing the Angle will reduce the effective limitation of the polymer, but the more prone to leakage.
3, the width of the screw edge: generally 7 mm, 11 mm, 11.2 mm, 14 mm, 19 mm and so on, which is to measure the shear size and mixing size of one of the most important parameters.
The larger the width, the larger the shear, the smaller the mixing; The smaller the width, the smaller the shear and the larger the mix.
4, head number: general single head, double head, three first-class type.
Ⅰ. In the forward direction, the smaller the number of heads, the greater the extrusion conveying capacity, the greater the torque, the better the mixing characteristics, but the less the shear action.
Ⅱ. The lower the number of heads, the smaller the extrusion conveying capacity and the better the mixing characteristics.
“M” series: tooth shape, mainly play a disturbing material flow, can accelerate the material homogenization. The more teeth, the stronger the mix. However, attention should be paid to the use of high shear damage.

Five, Temperature setting of each section
1, conveying section temperature
Should not be too high, affect the material transport and shear in this section. Also should not be too low, screw force is too large or stuck. Generally slightly fused, arranged in a gradient.
2, Melting stage temperature
(1) Glass fiber system, the temperature is too low, the resin is half melted, and the glass fiber coating is poor to the back section; The temperature is too high, the resin flow is improved, mixing and shear action becomes small, and even high temperature degradation, its setting principle: deduct the heat input of screw shear, slightly higher than the melting point range of the base material.
(2) Filling system, (provide strong shear to make the filling material, fully dispersed), melting section is 10~20℃ higher than the melting point of the base material (as far as possible), so that the material is fully fused and evenly distributed.
(3) Flame retardant, (protect the flame retardant), the temperature should be low, especially the white material, as far as possible to reduce.
(4) Glass fiber reinforced flame retardant system, set the temperature between the first two, based on the basic melting point of the material.
(5) Alloy system, based on the melting temperature of the two groups, and considering the proportion of components and the heat sensitivity of the group, the temperature is adjusted appropriately.
3, mixing section temperature
A, glass fiber system, the temperature is too low, the material flow performance is poor, the viscosity is large, the friction becomes large, the heat generation is high, will appear local overheating; If the temperature is too high, the resin will degrade and the shear degree of glass fiber will become worse. The setting principle is slightly higher than the melting point range of the base material.
B, filling system, (provide strong shear to make filling material, fully dispersed), mixing section is higher than the melting point of the base material 10~20℃ (as far as possible), so that the material is fully molten uniform distribution, ensure that the mixture is fluid state.
C, flame retardant system, (protect the flame retardant) blending temperature in the low, especially the white material, as far as possible to reduce.
D. Glass fiber reinforced flame retardant system, the temperature setting is based on the basic melting of the material, protect the flame retardant.
E. Blending, based on the melting temperature of components, and considering the proportion of components and components of heat sensitivity to adjust.
4. Temperature of homogenization (material quantity) section
To reduce the temperature properly, but die head high temperature conducive to discharge. On the basis of melting temperature, the temperature should be reduced appropriately.
Six, Speed problem
The higher the rotational speed, the larger the shear, the finer the size of the dispersed phase, but the rotational speed is too large, the friction is easy to cause thermal degradation, and the residence time is shorter, and the mixing is uneven. The lower the rotational speed, the smaller the shear, the uneven dispersion, and the longer residence time, which is unfavorable to the easily decomposed polymer.
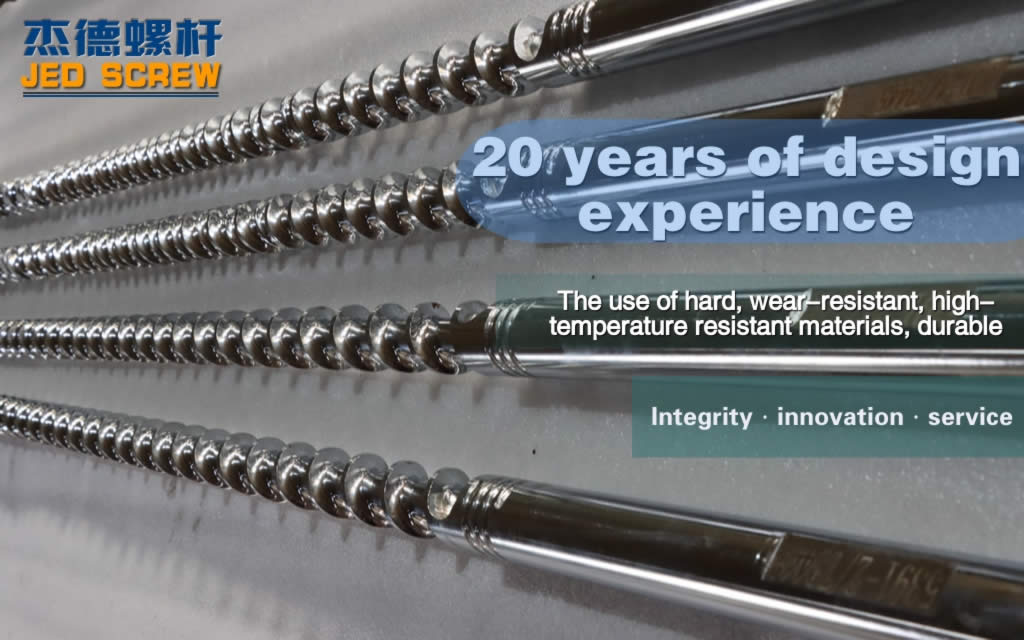
Understand the relevant knowledge of plastic extruder, we know the importance of screw selection, the appropriate screw barrel can improve production efficiency, increase enterprise benefits. Zhoushan Jed Machinery Co., LTD has modern technology, advanced plant and equipment, can design and manufacture various types and uses of screw barrel according to customer needs, good after-sales service to let you feel at ease, rest assured, satisfied. Jed mechinery help your enterprise better take-off, and you achieve a better future together.
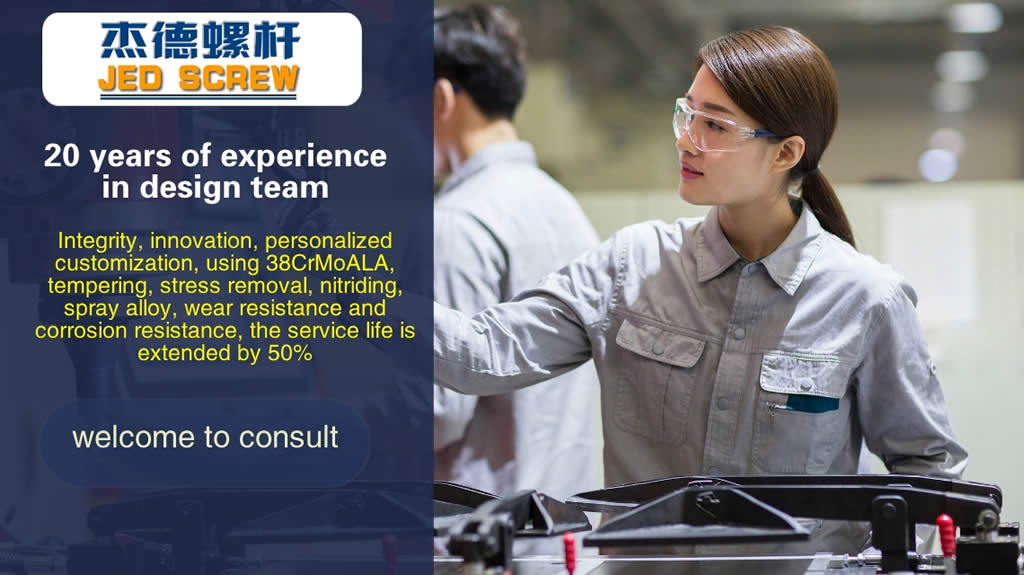
WhatsApp
Scan the QR Code to start a WhatsApp chat with us.