1. Back pressure is too high: If the back pressure is set too high, the screw may not have enough pressure to transport the melt forward to overcome the back pressure of the back pressure, and the screw will rotate in a certain direction without retreating, so It will do more work on the melt and significantly increase the melt temperature, which will adversely affect the quality of the finished product and the cycle time.
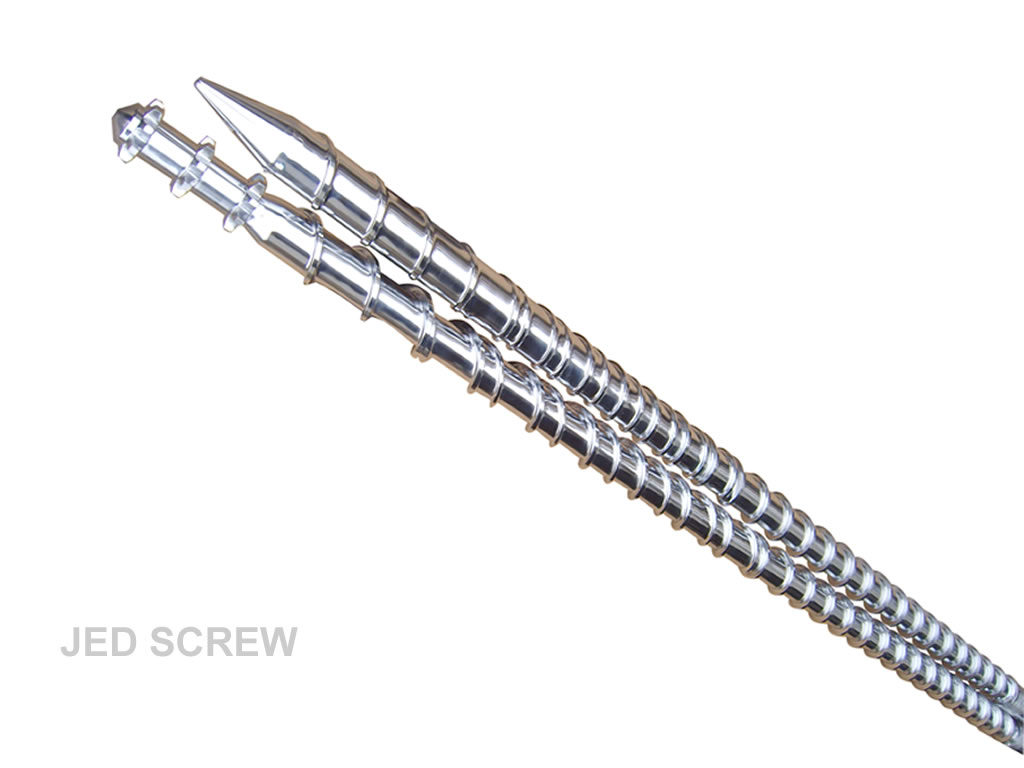
2. Overheating or overcooling in the back half of the barrel: At the back of the feeding section, the material forms a thin layer of molten polymer during the process of heating and shrinking. The molten film layer is attached to the barrel. Without this thin layer, bimetallic screw barrel the pellets are difficult to transport forward. The material in the feeding section must be heated to a critical temperature in order to produce the critical molten film. However, it is often that the residence time of the material in the barrel is too short to allow the polymer to reach this temperature. This situation may be caused by the small scale of the equipment and the correspondingly equipped barrel and screw. If the residence time is too short, it is easy to cause the polymer to melt or mix insufficiently, which will cause the screw to slip or stop.
3. Cylinder or screw wear: Same as the feeding section, when the resin is melted in the screw compaction section, it adheres to the barrel wall. When the screw rotates, the material is separated from the barrel wall and transported forward after being subjected to shearing force. If there are wear areas on the screw and barrel, the screw cannot effectively transport materials forward.
4. Improper hopper planning: Correct hopper planning is the key to ensuring stable delivery of materials. Generally speaking, new pellets of uniform size work well in a square hopper with a sudden compaction zone. However, this is not the case when participating in recycled materials. By destroying again the shape and size of the pellets are very different, which will affect the uniformity of the feed. Incoherent feed means that the screw cannot maintain a uniform conveying pressure on the melt, and slippage occurs.
5. When processing hygroscopic materials: Incorrect drying of materials will significantly reduce the viscosity of materials in the barrel and generate water vapor, making it difficult for the screw to transport materials forward.
6. Failure of the non-return ring: When the screw is rotating and plasticizing materials, the non-return ring should be in the front position and contact the fixed ring seat. If the non-return ring is in a backward state, or a state between forward and backward, the molten polymer will have resistance when passing through the gap between the non-return ring and the ring seat. If you suspect that there is a problem with the non-return ring, replace it immediately.
WhatsApp
Scan the QR Code to start a WhatsApp chat with us.