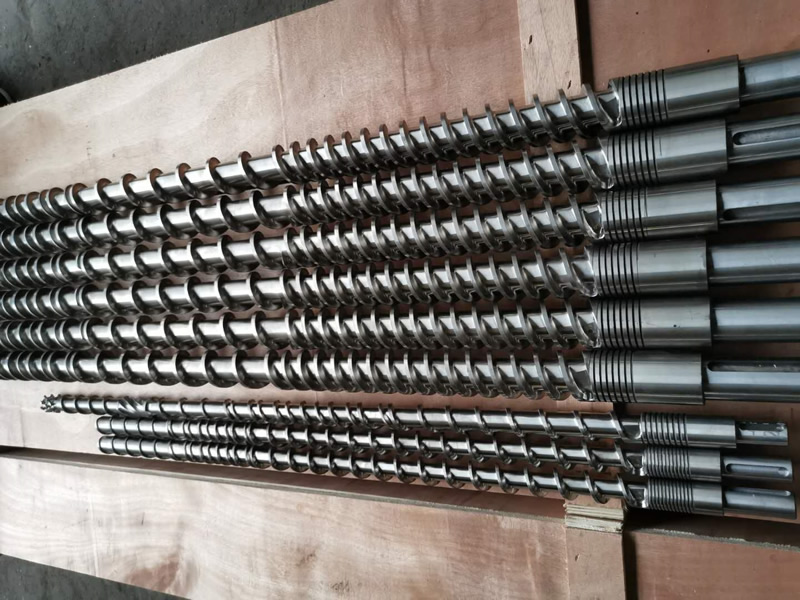
Every kind of plastic has an ideal plasticizing processing temperature range, and the processing temperature of the barrel should be controlled to make it close to this temperature range. Granular plastic enters the barrel from the hopper and first reaches the feeding section. Dry friction will inevitably occur in the feeding section. When these plastics are not heated enough and melted unevenly, it is easy to increase the abrasion of the inner wall of the barrel and the surface of the screw.
Similarly, in the compression section and the homogenization section, if the molten state of the plastic is disordered and uneven, it will also cause increased wear.
The speed should be adjusted properly. Because some plastics are added with strengthening agents, such as glass fibers, minerals or other fillers. The friction of these substances on metal materials is often much greater than that of molten plastics. When injection molding these plastics, if they are made with a high rotation speed, it will increase the shearing force to the plastic, and at the same time, the reinforcement will produce more shredded fibers. The shredded fibers contain sharp ends, causing wear Power is greatly increased.
When inorganic minerals slide at high speed on the metal surface, their scraping effect is not small. Therefore, the speed should not be adjusted too high.
To remove debris in the plastic. Generally speaking, there is no debris in the fresh plastic purchased originally, but after transportation, weighing, drying, color mixing, and especially adding recycled materials, it may be mixed with debris.
It is as small as metal scraps, as large as heating coil nuts, paper clips, and even a bunch of warehouse keys. It has been mixed into the barrel. The damage to the screw is self-evident (the barrel will also be damaged at the same time. ), so it is necessary to install a magnet holder, and strictly manage and monitor the feeding.
The water content in the plastic has a certain effect on the wear of the screw surface. If the plastic is not completely drained of water before injection, when the remaining water enters the screw compression section, it will form “steam particles” with high temperature and pressure that are previously melted and mixed in the molten plastic. As the screw advances during the injection process, the From the chemical section to the head of the screw, these “steam particles” relieve pressure and expand during the injection process, just like tiny impurity hard particles, which have frictional damage to the wall.
WhatsApp
Scan the QR Code to start a WhatsApp chat with us.