An injection molding machine usually has three screws to choose from, called A, B, and C screws, with small, medium, and large diameters. Their aspect ratios are about 22, 20, and 18.
The screw length and the injection stroke of an injection molding machine may seem to be two different things at first glance. In fact, there is a subtle “quality and quantity” relationship between the two, and the ratio is a qualitative measure.
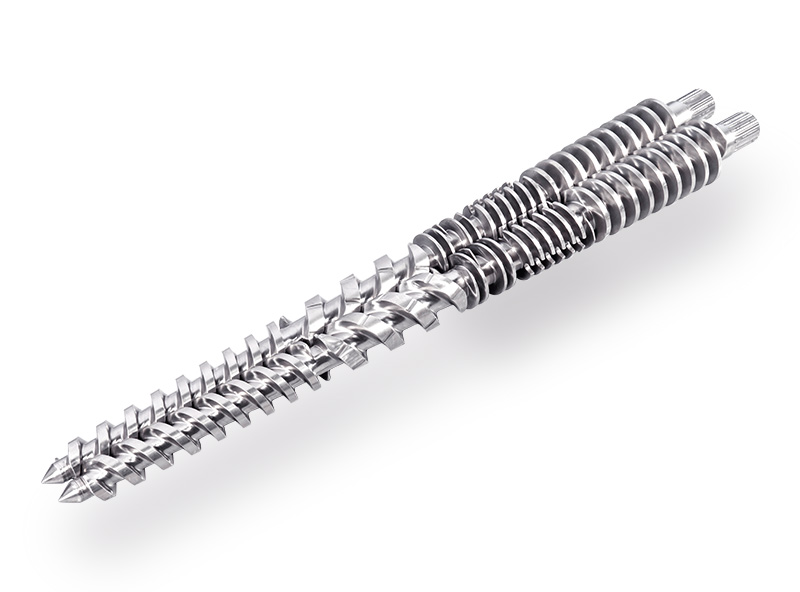
The length of the screw is generally not measured in absolute length, but in length relative to the diameter. In this way, screws of different diameters can also be compared in length. This length is called the aspect ratio, represented by L/D. The length of the screw is of course only the part with the thread. A more accurate algorithm is to calculate the center line of the hopper, which is called the effective length or effective aspect ratio.
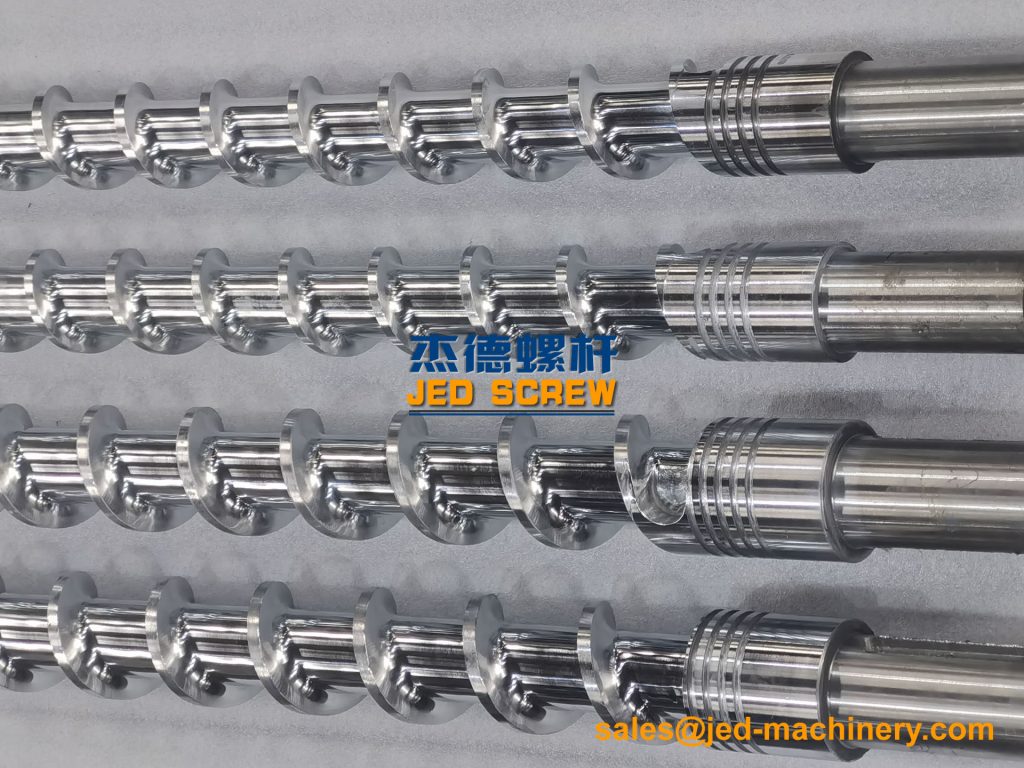
The plasticized plastic is called melting and is stored at the top of the injection screw barrel, ready to be used in the next injection. The ideal melting is uniform in temperature. But in general, this is not the case. Since the heating tile does not surround the barrel by 360°, but has a gap, the circumferential temperature is not uniform. The heat of the heating tile is transferred from the outside to the inside, and the melting heat transfer is not good, so the radial temperature is not uniform.
When plasticizing, the screw retreats. The effective length is therefore gradually reduced. The larger the feeding stroke (injection stroke), the greater the effective length change, and the more uneven the axial temperature. Readers who are familiar with extruders know that the extruder screw does not go back. Therefore, the extrusion melting has no axial temperature difference. If the melting temperature differs by 15°C, the appearance and mechanical properties of the finished product will not be even. Multi-cavity molds will produce differences in the finished product between cavity and cavity, even one cavity is not full, one cavity is flashed, and this situation is irregular.
To improve this situation, the injection stroke should be designed to be 4 times the diameter of the B screw. The change in the effective aspect ratio is therefore 4. In this case, the injection stroke is 4.4 times the diameter of the A screw and 3.7 times the diameter of the C screw. The radial temperature difference is the largest with screw A and the smallest with screw C.
Increasing the aspect ratio will reduce the axial temperature difference. The reason is that the screw is longer, and the plastic has to turn a few more times before it reaches the end of the screw. Stir more, the temperature will be more even. In the case of the same injection stroke, the longer the screw, the “injection stroke ÷ screw length” decreases, so the axial temperature difference also decreases. If the B screw can have an aspect ratio of 22, it is of course better than the aspect ratio of 20.
In general, a design with a large injection stroke or a short screw length-to-diameter ratio will have a large injection weight, but the melting axial temperature will be uneven, which is only suitable for single-cavity products with low requirements. The design that limits the injection stroke and the large screw length-to-diameter ratio ensures the quality of multi-cavity products.
WhatsApp
Scan the QR Code to start a WhatsApp chat with us.